4.1 Allgemeines (nach oben)
4.1.1 Übersicht von austenitischen Edelstählen
Der Begriff "Edelstahl Rostfrei" ist ein Oberbegriff für ca.
120 verschiedene Sorten von nicht-rostenden Stählen.
Über Jahrzehnte wurde eine Vielzahl von verschiedenen Legierungen entwickelt,
welche für die verschiedene Anwendungen die jeweils besten Eigenschaften
liefern. Diese Legierungen haben alle ein gemeinsames Merkmal: Sie benötigen
durch das in der Legierung enthaltene Chrom keinen zusätzlichen Oberflächenschutz.
Dieser Chromanteil bildet auf der Oberfläche eine farblose, transparente
Oxydschicht, welche sich nach Beschädigung der Oberfläche mit Hilfe
des in der Luft oder Wasser enthaltenen Sauerstoff selbsttätig schließt.
Nichtrostende Stähle sind in der DIN 17440 und der DIN EN ISO 3506 zusammengefasst.
Grundsätzlich werden Edelstahllegierungen nach ihrem kristallinen Gefüge
in 4 verschiedene Hauptgruppen eingeteilt:
Nichtrostende Stähle mit niedrigem Kohlenstoffgehalt (von höchstens
0,03 %) dürfen
zusätzlich mit dem Buchstabel "L" gekennzeichnet werden (Beispiel:
A4L - 80).
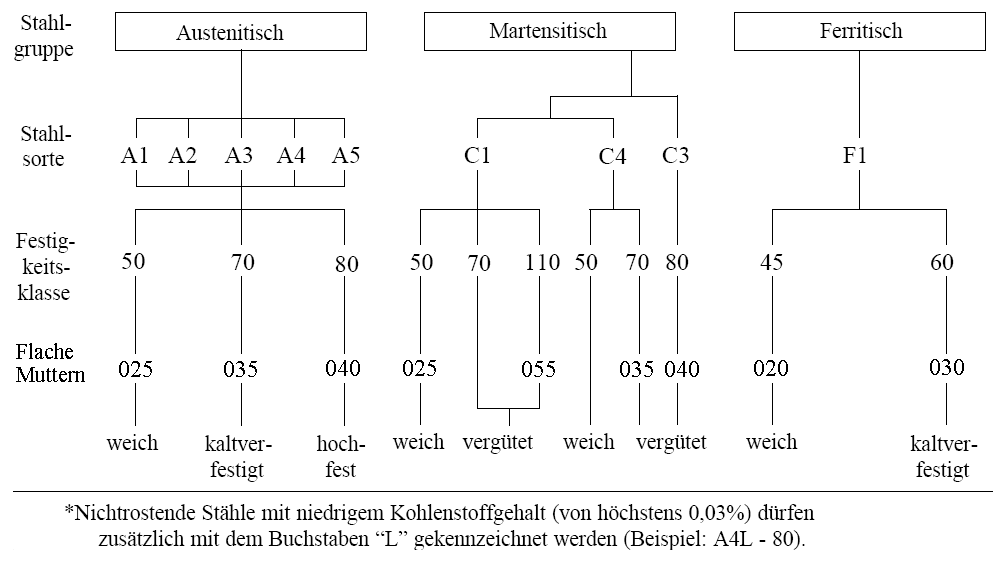
Abbildung 5 - aust. Edelstähle
Martensitische Edelstähle
Sind Stähle mit 10,5 - 13,0% Chromanteil und einem Kohlenstoffgehalt von
0,2 - 1,0%
Es können weitere Elemente als Legierungsanteil zugefügt werden. Das
Verhältnis zum Kohlenstoff muss eine Wärmebehandlung, das so genannte
Vergüten, zulassen. Dadurch werden Festigkeitssteigerungen möglich.
Ferritische Edelstähle (sog. Chrom - Stähle)
Sind Stähle mit 12,0 - 18,0% Chromanteil und sehr geringem Kohlenstoffgehalt
kleiner 0,2%.
Diese sind nicht härtbar.
Austenitische Edelstähle (sog. Chrom - Nickel / Chrom - Nickel
- Molybdän Stähle)
Die austenitischen Chrom-Nickel Stähle bieten eine besonders günstige
Kombination von Verarbeitbarkeit, mechanischen Eigenschaften und Korrosionsbeständigkeit.
Sie eignen sich daher für viele Anwendungsmöglichkeiten und sind die
wichtigste Gruppe nichtrostender Stähle. Die wichtigste Eigenschaft dieser
Stahlgruppe ist die hohe Korrosionsbeständigkeit, die mit zunehmendem Legierungsgehalt,
besonders an Chrom und Molybdän, gesteigert wird. Wie bei den ferritischen
Stählen, ist auch bei den austenitischen Stählen zum Erreichen guter
technologischer Eigenschaften ein feinkörniges Gefüge notwendig.
Als abschließende Wärmebehandlung wird ein Lösungsglühen
bei Temperaturen zwischen 1000° C und 1150° C mit anschließender
Abkühlung in Wasser oder Luft durchgeführt, um die Ausbildung von
Ausscheidungen zu vermeiden. Austenitische Stähle sind im Gegensatz zu
martensitischen Stählen nicht härtbar. Das hohe Dehnungsvermögen
der austenitischen Stähle garantiert eine gute Kaltumformbarkeit.
4.1.2 verschiedene Typen von Edelstählen (nach oben)
Typ |
Werkstoff-Nr. |
Beschreibung |
Beständigkeit |
Schweissbarkeit | |
gegen
|
gegen Säure |
|
|||
A1 |
1.4300 |
=
klassicher Drehstahl |
mittel |
gering |
gering |
A2 |
1.4301 |
= klassicher Edelstahl |
hoch |
gering |
gut |
A3 |
1.4306 |
|
hoch |
mittel |
gut |
A4 |
1.4401 |
= Edelstahl für Hochsäureumgebungen |
hoch |
hoch |
gut |
A5 |
1.4436 |
= Edelstahl mit besonderer Härte, nur gegen Anfrage. |
hoch |
hoch |
gut |
4.2 Zusammensetzung von Edelstahl (nach oben)
4.2.1 chemische Zusammensetzung von Edelstahl (nach oben)
Stahl- gruppe Material |
Für Schrauben/Muttern übliche Werkstoffe |
Cr**
|
Ni**
|
Mo**
|
C**max.
|
Si** max.
|
Mn** max.
|
P** max.
|
S** max.
|
Sonstige Zusätze Anmerkungen |
|
Werkstoff-Nr. (AlSI-Nr.) |
Werkstoff-Kurzname n. EN 10088-3/DIN 17006, 17440 |
||||||||||
(Details siehe ISO 3506, Tab. 1) | |||||||||||
A 1 | 1.4305 (303) | X8CrNiS 18-9 |
16-19
|
5-10
|
0,7
|
0,12
|
1,0
|
6,5
|
0,20
|
0,15-0,35
|
Cu, - Schwefel darf durch Selen ersetzt werden |
A 2 | 1.4301 (304) 1.4303 (305) | X5CrNi 18-10 |
15-20
|
8-19
|
*
|
0,10
|
1,0
|
2,0
|
0,05
|
|
* Mo zulässig |
A 3 | 1.4541 (321) | X6CrNiTi 18-10 |
17-19
|
9-12
|
*
|
0,08
|
0,045
|
0,03
|
* Mo zulässig - muss zur Stabilisierung Ti oder Nb oder Ta enthalten | ||
A 4 | 1.4401 (316) | X5CrNiMo 17-12-2 |
16-18,5
|
10-15
|
2,0 3,0
|
0,08
|
1,0
|
2,0
|
0,045
|
0,03
|
Muss zur Stabilisierung Ti oder Nb oder Ta enthalten |
A 5 | 1.4571 (316 Ti) |
X6CrNiMoTi 17-12-2 |
10,5-14
|
||||||||
A - | 1.4439 | X2CrNiMoN 17-13-5 |
16,5-18,5
|
12,5-14,5
|
4,0-
|
0,03
|
1,0
|
2,0
|
0,045
|
0,015
|
Austenitische / austenitisch-ferritische Stähle mit besonderer Beständigkeit gegen chloridinduzierte Spannungsrisskorrosion - z.B. in Hallenschwimmbädern |
A - | 1.4539 | X1NiCrMoCu 25-20-5 |
19-21
|
24-26
|
5,0
|
0,02
|
0,7
|
|
0,030 |
0,010
|
|
A - | 1.4529 |
X1NiCrMoCuN 25-20-7 |
6,0-7,0
|
0,5
|
1,0 |
||||||
A/F - | 1.4462 |
X2CrNiMoN 22-5-3 |
21-23
|
4,5-6,5
|
2,5-3,5
|
0,03
|
1,0
|
2,0 |
0,035
|
0,015
|
|
C - | 1.4034 (420) |
X46Cr 13 |
12,5-14,5
|
0,43-
0,50 |
1,0
|
1,0 |
0,040
|
0 ,03
|
Werkstoffe für federnde Teile - z.B. nach DIN 127, 128, 471, 472, 2093, 6797, 6798, 6799, 7967, 7980 |
||
C - |
1.4122 |
X39CrMo 17-1 |
15,5- 17,5
|
≤ 1,0
|
0,80- 1,30
|
0,33-
0,45 |
1,0
|
1,5
|
0,040
|
0,03
|
|
A - | 1.4310 (301) | X10CrNi 18-8 |
16-18
|
6-9,5
|
≤ 0,8
|
0,05-
0,15 |
2,0
|
2,0
|
0,045
|
0,015
|
(Achtung: reduzierte Federkräfte gegenüber Federstahl) |
C - | 1.4568 (301) | X7GNiAl 17-7 |
16-1
|
6,5-7,8
|
0,09
|
0,7
|
1,0
|
0,04
|
0,015
|
Al 0,70-1,5 |
(Chemische Zusammensetzung in % nach ISO 3506 / EN 10088-3.)
**Chrom, Nickel, Molybdän, Kohlenstoff, Silizium, Mangan, Phosphor, Schwefel
(Details siehe Kapitel 4.2.2 chemische Elemente von Edelstahl)
Tabelle 28: chem. Zusammensetzung Edelstahl
Tabelle 29: Kurzform (Edelstahlklasse A1-A5 - handelsüblich)
Stahlgruppe |
Stahlsorte |
Chemische Zusammensetzung (Massenanteil in %)1) |
|||||||||
C* |
Si* |
Mn* |
P* |
S* |
Cr* |
Mo* |
Ni* |
Cu* |
Anmerkungen |
||
Austenitisch |
A1 |
0,12 |
1 |
6,5 |
0,2 |
0,15 bis 0,35 |
16
bis 19 |
0,7 |
5
bis 10 |
1,75
bis 2,25 |
2), 3) 4) |
A2 |
0,1 |
1 |
2 |
0,05 |
0,03 |
15
bis 20 |
-5) |
8
bis 19 |
4 |
6), 7), 8) |
|
A3 |
0,08 |
1 |
2 |
0,045 |
0,03 |
17
bis 19 |
-5) |
9
bis 12 |
1 |
6), 9) |
|
A4 |
0,08 |
1 |
2 |
0,045 |
0,03 |
16
bis 18,5 |
2
bis 3 |
10
bis 15 |
1 |
10), 8) |
|
A5 |
0,08 |
1 |
2 |
0,045 |
0,03 |
16
bis 18,5 |
2
bis 3 |
10,5
bis 15 |
1 |
9), 10) |
Bitte beachten Sie folgende Anmerkungen:
(1) Maximalwerte, soweit nicht andere Angaben gemacht sind.
(2) Schwefel darf durch Selen ersetzt werden.
(3) Falls der Massenanteil an Nickel unter 8% liegt, muss der Massenanteil an
Magan mindestens 5% betragen.
(4) Für den Massenanteil an Kupfer gibt es keine Mindestgrenze, sofern
der Massenanteil an Nickel mehr als 8% beträgt.
(5) Molybdän ist nach Wahl des Herstellers zulässig. Falls dennoch
für bestimmte Anwendungen eine Einschränkung des Molybdängehaltes
notwendig ist, muss dies vom Kunden bei der Bestellung festgelegt werden.
(6) Molybdän ist nach Wahl des Herstellers ebenfalls zulässig.
(7) Falls der Massenanteil an Chrom unter 17% liegt, sollte der Massenanteil
an Nickel mindestens 12% betragen.
(8) Bei austenitischen Stählen mit einem Massenanteil an Kohlenstoff von
max. 0,03% darf Stickstoff bis max. 0,22% enthalten sein.
(9) Muss zur Stabilisierung Titan 5 x C bis max. 0,8% enthalten und entsprechend
nach dieser Tabelle gekennzeichnet sein, oder muss zur Stabilisierung Niob und/oder
Tantal 10 x C bis max. 1% enthalten und entsprechend nach dieser Tabelle gekennzeichnet
sein.
(10) Der Kohlenstoffgehalt darf nach Wahl des Herstellers höher liegen,
soweit dies bei größeren Durchmessern zum Erreichen der festgelegten
mechanischen Eigenschaften erforderlich ist, jedoch bei austenitischen Stählen
nicht über 0,12%.
* Kohlenstoff, Silizium, Mangan, Phosphor, Schwefel, Chrom, Molybdän, Nickel, Kupfer (Details siehe Kapitel 4.2.2 chemische Elemente von Edelstahl)
4.2.2 chemische Elemente in Edelstählen (nach oben)
Edelstähle können folgende Elemente beinhalten:
Name,
Symbol, |
Beschreibung |
Aluminium
|
Aluminium
wirkt stark desoxidierend und denitrierend. Die Bildung von harten Al-Nitriden
reduziert die Alterungsanfälligkeit von Stahl. Bei ferritischen Chromstählen
führt die Beigabe von Aluminium neben verbesserter Zunderbeständigkeit
zu einer verringerten Empfindlichkeit gegenüber interkristalliner
Korrosion. |
Chrom |
Chrom
erhöht die Zugfestigkeit durch Bildung von Mischkristallstrukturen
und reduziert die kritische Abkühlgeschwindigkeit. Dadurch steigen
Zunderbeständigkeit und Einhärtetiefe. Bei ferritischen- (Klasse
C) und austenitischen Stählen (Klasse A) ab einem Anteil von von
13% korrosionshemmend. Grund ist die die Bildung einer resistenten Chromoxid-Schicht
auf der Oberfläche. |
Cobalt |
Cobalt verbessert die Anlassbeständigkeit und steigert die Warmfestigkeit von Stählen. |
Kohlenstoff |
Kohlenstoff
erhöht bei Stählen die Härte und Festigkeit. Ein zu hoher
Kohlenstoffanteil bewirkt jedoch eine starte Reduktion der Kaltformbarkeit. |
Mangan |
Mangan
erhöht bei Stählen die Zähigkeit und Festigkeit. Durch
die Bindung von Schwefel als Mangansulfid reduziert es bei hoher Konzentration
die Verformungsfähigkeit senkrecht zur Walzrichtung. |
Molybdän |
Eine
Molybdänkonzentration von über 0,2 % erhöht
die Durchhärtbarkeit von Stählen. Zudem wird Anlassversprödung
reduziert. Molybdän wirkt bei hohen Temperaturen gefügestabilisierend
und wird daher meist in Stählen für hohe Betriebstemperaturen
verwendet. |
Nickel |
Nickel
ist Hauptbestandteil und gewichtiger Preisfaktor in der Legierung von
nichtrostenden Stählen der Klasse A (austenitischer Stähle:
A1, A2, A3, A4, A5). Nickel bewirkt sehr hohe Zähigkeit, auch bei
niedrigen Temperaturen. Es ist besonders für die Vergütung großer
Querschnitte geeignet, da hier hohe Festigkeits- und optimale Zähigkeitswerte
erzielt werden. Eine alleinige Anwendung von Nickel ist nicht vorteilhaft,
da es anlassversprödend wirkt. Daher wird Nickel meist zusammen mit
Molybdän verwendet. |
Niob |
Niob
wird bei austenitischen Stählen (z.B. A3 oder A5) zur Verbesserung
der Stabilität beigefügt. |
Phosphor |
Phosphor
bewirkt Kaltsprödigkeit und Empfindlichkeit gegen Schlagbeanspruchung.
Zudem reduziert es die Zähigkeit von Stählen. Ziel ist ein minimaler
Phosphorgehalt. |
Schwefel |
Als
Nachbarelement von Phosphor gilt es auch, den Schwefelanteil in Stählen
möglichst gering zu halten. Die Bildung von Mangansulfid erhöht
den Schmelzpunkt des Stahl, was die Rot- und Heißbruchgefahr reduziert.
Bei manchen Automatenstählen wird Schwefel beigesetzt, um kurzbrüchige
Späne zu erreichen. |
Silizium |
Silizium erhöht die Zunderbeständigkeit und trägt zur Stahlberuhigung bei, wodurch es die Alterungsbeständigkeit und Zähigkeit von Stählen erhöht. |
Stickstoff |
Die
Beigabe von Stickstoff stabilisiert das Austenitgefüge. Durch Nitridausscheidungen
wird dadurch die Festigkeit erhöht und zudem verbessert man die mechanischen
Eigenschaften bei hoher Temperatur. Jedoch kann die Nitridabgabe zu Alterung
und Reduktion der Zähigkeit führen. Bei unlegierten und geringlegierten
Stählen erhöht sich die Empfindlichkeit gegenüber interkristalliner
Korrosion. |
Tantal |
Tantal wird bei austenitischen Stählen (z.B. A3 oder A5) zur Verbesserung der Stabilität beigefügt. |
Titan |
Titan wirkt
denitrierend, desoxidierent, schwefelbindend und erzeugt Karbid. Dadurch
hemmt Titan bei nichtrostenden Stählen die interkristalline Korrosion.
|
Vanadium |
Vanadium
verbessert die Zähigkeit von Stählen. Grund ist die Bildung
von Karbiden, welche bereits bei einem Anteil von 0,1% Vanadium im Werkstoff
die Anlassversprödung reduzieren. |
Wasserstoff |
Wasserstoff gelangt während der Herstellung und Oberflächenbehandlung in den Stahl und schädigt diesen durch Wasserstoffversprödung. Temperung bewirkt ein Austreten des Wasserstoffs aus dem Stahl. |
Tabelle 30: chem. Elemente von Edelstahl
4.3 Beständigkeit von Edelstahl (nach oben)
Chemische Beständigkeit von Verbindungselementen aus nichtrostenden Stählen A 2 und A 4
Die Beständigkeitsangaben können sich in der Praxis verändern; selten wirken die reinen Agenzien, oft verstärken oder schwächen Beimengungen den Angriff. Auch Rückstände am Teil können die Bedingungen verändern. Der sicherste Weg ist die Untersuchung unter Betriebsbedingungen.
1 - beständig (Substanzverlust weniger als 0,1 g/m2 x h)
2 - bedingt beständig (Substanzverlust von 0,1 bis 1,0 g/m2 x h)
3 - wenig beständig (Substanzverlust von 1,0 bis 10,0 g/m2 x h)
4 - unbeständig (Substanzverlust über 10,1 g/m2 x h)
Agenzien |
Beständigkeitsgrad |
Agenzien |
Beständigkeitsgrad |
||
|
A 2 |
A 4 |
|
A 2 |
A 4 |
Abwässer ohne Schwefelsäure |
1 |
1 |
Latex |
1 |
1 |
Aceton, alle Konz. |
1 |
1 |
Leimöl |
1 |
1 |
Aethyläther, kochend |
1 |
1 |
|||
Aethylacetat |
1 |
1 |
Magnesiumsulfat |
1 |
1 |
Aethylalkohol, alle Konz. |
1 |
1 |
Maleisäure |
1 |
1 |
Alaun (10 %), kalt |
1 |
1 |
Melasse |
1 |
1 |
gesättigte Lösung, kochend |
2 |
1 |
Methylalkohol |
1 |
1 |
Aluminiumacetat |
1 |
1 |
Milchsäure, kalt |
1 |
1 |
Aluminiumsulfat (10 %), kalt |
1 |
1 |
Milchsäure, alle Konz., kochend |
3 |
2 |
gesättigt, kalt |
2 |
1 |
|||
Ameisensäure, kalt |
1 |
1 |
Natriumaluminat |
1 |
1 |
Ammoniumkarbonat |
1 |
1 |
Natriumbisulfat, kochend |
1 |
1 |
Ammoniumnitrat |
1 |
1 |
Natriumbisulfid, kochend |
1 |
1 |
Ammoniumsulfat, kalt |
1 |
1 |
Natriumkarbonat (Soda) |
1 |
1 |
Ammoniumsulfit |
1 |
1 |
Natriumhydroxyd, kalt |
1 |
1 |
Anilin |
1 |
1 |
Natriumnitrat |
1 |
1 |
Natriumperchlorat |
1 |
1 |
|||
Benzin |
1 |
1 |
Natriumphosphat |
1 |
1 |
Benzoesäure |
1 |
1 |
Natriumsulfat |
1 |
1 |
Benzol |
1 |
1 |
Natriumsulfid |
1 |
1 |
Bier |
1 |
1 |
Natriumsulfit |
1 |
1 |
Blausäure |
1 |
1 |
Nickelsulfat |
1 |
1 |
Borsäure |
1 |
1 |
Nitrosesäure |
2 |
1 |
Butylacetat |
1 |
1 |
|||
Öle (Schmier- und vegetabilische Öle) |
1 |
1 |
|||
Calziumbisulfit, kalt |
1 |
1 |
Oxalsäure, 5 %, kalt |
1 |
1 |
kochend |
3 |
1 |
|||
Calziumhydroxyd (10-50 %), kalt |
1 |
1 |
Phenol, kochend |
2 |
1 |
Calziumnitrat |
1 |
1 |
Phosphorsäure bis 70 %, kalt |
1 |
1 |
Chlor, trocken |
1 |
1 |
Photograph. Entwickler/Fixierbad |
1 |
1 |
Chloroform, wasserfrei |
1 |
1 |
Pottasche |
1 |
1 |
Chlorschwefel, wasserfrei |
1 |
1 |
|||
Chromsäure (10 %), kalt |
1 |
1 |
Quecksilber |
1 |
1 |
kochend |
3 |
2 |
Quecksilberamalgam |
1 |
1 |
Cyankalium |
1 |
1 |
Quecksilbernitrat |
1 |
1 |
Eisennitrat |
1 |
1 |
Salicylsäure |
1 |
1 |
Eisensulfat |
1 |
1 |
Salmiakgeist |
1 |
1 |
Entwickler (Foto) |
1 |
1 |
Salpetersäure bis 60 %, kalt |
1 |
1 |
Essigsäure, kalt |
1 |
1 |
Schwefel (geschmolzen) |
1 |
1 |
Schwefeldioxyd |
1 |
1 |
|||
Fettsäure, 150°C |
1 |
1 |
Schwefelkohlenstoff |
1 |
1 |
Flüssige Gase (Propan, Butan) |
1 |
1 |
Schwefelwasserstoff |
1 |
1 |
Formalin |
1 |
1 |
Schweflige Säure, gesättigt, 20° C |
1 |
1 |
Fruchtsäfte |
2 |
1 |
Seife |
1 |
1 |
Gerbsäure |
1 |
1 |
Teer |
1 |
1 |
Glyzerin |
1 |
1 |
Tetrachlorkohlenstoff, wasserfrei |
1 |
1 |
Trichloraethylen, wasserfrei |
1 |
1 |
|||
Kaliumbichromat (25 %) |
1 |
1 |
|||
Kaliumbitartrat, kalt |
1 |
1 |
Viskose |
1 |
1 |
Kaliumchlorat |
1 |
1 |
|||
Kaliumhydroxyd (Kalilauge) |
1 |
1 |
Wasserglas |
1 |
1 |
Kaliumnitrat |
1 |
1 |
Wasserstoffsuperoxyd |
1 |
1 |
Kaliumpermanganat |
1 |
1 |
Wein |
1 |
1 |
Kalkmilch |
1 |
1 |
Weinsäure |
1 |
1 |
Kaliumsulfat |
1 |
1 |
|||
Kampfer |
1 |
1 |
Zinksulfat |
1 |
1 |
Kohlendioxyd |
1 |
1 |
Zitronensäure, gesättigt, kalt |
1 |
1 |
Kreosot |
1 |
1 |
Zitronensäure, 50 %, kochend |
4 |
1 |
Kupferacetat |
1 |
1 |
Zuckerlösung |
1 |
1 |
Kupferarsenit |
1 |
1 |
|||
Kupfernitrat |
1 |
1 |
|||
Kupfersulfat |
1 |
1 |
Tabelle 31: chem. Beständigkeit von Edelstählen A2, A4
4.4 Mechanische Eigenschaften von Edelstahl (nach oben)
4.4.1 Anziehdrehmomente von Edelstahlschrauben (nach oben)
Anziehmomente für Schrauben und Muttern aus A 2/A 4
Bei Verbindungselementen aus nichtrostenden Stählen sind die Reibungswerte
im Gewinde und an den Auflageflächen wesentlich größer als bei
vergüteten Stahlschrauben - auch der Streubereich der Reibungswerte ist
hier viel größer (bis über 100 %!). Zur endgültigen Bestimmung
des richtigen Drehmomentes ist ein Versuch unter Einsatzbedingungen angeraten.
Durch Verwendung von Spezialschmiermitteln können zwar die Reibungszahlen
µ verringert werden - aber der sehr große Streubereich bleibt erhalten.
Die Tabelle enthält unverbindliche Richtwerte für verschiedene Reibungszahlen,
gültig für Schrauben und Muttern nach DIN 912, 931, 933 und 934 /
ISO 4762, 4014, 4017, 4032 aus nichtrostenden Stählen A2 und A4, in der
Festigkeitsklasse -70 (kaltverfestigt = Kaltpressfertigung) bis zu Nennlängen
8 x d, bei Raumtemperatur (ca. + 20 °C) und einer Dehngrenzen-Ausnutzung
von Rp 0,2 = 90 %.
Die in der folgenden Tabelle genannten Anziehmomente können nur als
sehr grobe und unverbindliche Richtwerte verstanden werden - siehe VDI 2230!
Anziehmomente MA/Nm für A 2, A 4 -70 (-50**)
Reibungs zahl µ |
-70 = Rp 0,2 min. 450 N/mm2 |
**-50 = Rp 0,2 min. 210 N/mm2 |
|||||||||
M 4 |
M 5 |
M 6 |
M 8 |
M 10 |
M 12 |
M 16 |
M 20 |
M 24 |
M 27 |
M 30 |
|
0,10 |
1,7 |
3,4 |
5,9 |
14,5 |
30 |
50 |
121 |
244 |
234 |
328 |
445 |
0,12 |
2,0 |
3,8 |
6,7 |
16,3 |
33 |
56 |
136 |
274 |
264 |
371 |
503 |
0,14 |
2,2 |
4,2 |
7,4 |
17,8 |
36 |
62 |
150 |
303 |
290 |
410 |
556 |
0,16 |
2,3 |
4,6 |
7,9 |
19,3 |
39 |
66 |
162 |
328 |
314 |
444 |
602 |
0,18 |
2,5 |
4,9 |
8,4 |
20,4 |
41 |
70 |
173 |
351 |
336 |
475 |
643 |
0,20 |
2,6 |
5,1 |
8,8 |
21,5 |
44 |
74 |
183 |
370 |
355 |
502 |
680 |
0,30 |
3,0 |
6,1 |
10,4 |
25,5 |
51 |
88 |
218 |
439 |
421 |
599 |
809 |
0,40 |
3,3 |
6,6 |
11,3 |
27,6 |
56 |
96 |
237 |
479 |
458 |
652 |
881 |
Sechskantmuttern mit Klemmteil aus nicht-rostenden Stählen neigen manchmal wegen des hohen Gewindeflankendruckes beim Einformen des Bolzengewindes in das Klemmteil zum Festfressen. Hier hilft in der Regel die Behandlung des Bolzengewindes mit einem reibungsmindernden Mittel. Die veränderten Reibwerte sind beim Anziehen der Verbindung entsprechend zu berücksichtigen. | ![]() |
Die nachfolgenden Tabellen für die Werkstoffklassen A2 und A4 berücksichtigen
eine Reibungszahl
von µ = 0,10 für handelsübliche Schrauben und Muttern ohne Schmierung.
!! |
Zusätzliche Schmierung der Gewinde verändert die Reibungszahl erheblich und führt zu nicht bestimmbaren Anziehverhältnissen !. (vgl. Kapitel 4.4.6 Reibungszahlen bei Schmierung) |
!! |
- Klasse 50: für A2-50 und A4-50 ohne Längenbegrenzung (in der Regel
gedrehte Teile)
- Klasse 70: für A2-70 und A4-70 (handelsüblich) aber nur für
Längen mit 8 x Gewindedurchmesser
- Klasse 80: für A2-80 und A4-80 (stark kaltverfestigt) aber nur für
Längen mit 8 x Gewindedurchmesser
Gewinde |
Festigkeitsklasse
50 |
Festigkeitsklasse
70 |
Festigkeitsklasse
80 |
|||
Vorspannkraft |
Anziehdreh-moment |
Vorspannkraft |
Anziehdreh-moment |
Vorspannkraft |
Anziehdreh-moment |
|
M 3 |
900 |
0,85 |
1.000 |
1,0 |
1.200 |
1,3 |
M 4 |
1.080 |
0,8 |
2.970 |
1,7 |
3.960 |
2,3 |
M 5 |
2.260 |
1,6 |
4.850 |
3,4 |
6.470 |
4,7 |
M 6 |
3.200 |
2,8 |
6.850 |
5,9 |
9.130 |
8,0 |
M 8 |
5.860 |
6,8 |
12.600 |
14,5 |
16.700 |
19,3 |
M 10 |
9.320 |
13,7 |
20.000 |
30,0 |
26.600 |
39,4 |
M 12 |
13.600 |
23,6 |
29.100 |
50,0 |
38.800 |
67,0 |
M 14 |
18.700 |
37,1 |
40.000 |
79,0 |
53.300 |
106,0 |
M 16 |
25.700 |
56,0 |
55.000 |
121,0 |
73.300 |
161,0 |
M 18 |
32.200 |
81,0 |
69.000 |
174,0 |
92.000 |
232,0 |
M 20 |
41.300 |
114,0 |
88.600 |
224,0 |
118.100 |
325,0 |
M 22 |
50.000 |
148,0 |
107.000 |
318,0 |
143.000 |
424,0 |
M 24 |
58.000 |
187,0 |
142.000 |
400,0 |
165.000 |
534,0 |
M 27 |
75.000 |
- |
- |
275,0 |
- |
- |
M 30 |
91.000 |
- |
- |
374,0 |
- |
- |
M 33 |
114.000 |
- |
- |
506,0 |
- |
- |
M 36 |
162.000 |
- |
- |
842,0 |
- |
- |
Tabelle 33: Anziehdrehmomente Edelstahl
4.4.2 Festigkeit von Edelstahlschrauben (nach oben)
Mechanische Eigenschaften für Verbindungselemente der Stahlgruppen A
1 - A 5 bei ca. + 20° C.
Festigkeitsklasse |
Durchmes-serbereich |
Schrauben |
Muttern |
|||
Zugfestigkeit Rm N/mm2min |
0,2 % Dehngrenze Rp N/mm2min |
Bruchdehnung
A |
Prüfspannung Sp / N/mm2 min |
|||
m ≥ 0,8 d |
0,5 ≤ m < 0,8 d |
|||||
50 weich (gedreht) |
≤ M 39 |
500 |
210 |
0,6 d |
500 |
250 (Fkl. - 025) |
70 kaltverfestigt* (gepresst) |
≤ M 24 |
700 |
450 |
0,4 d |
700 |
350 (Fkl. - 035) |
80 stark kaltverfestigt* |
≤ M 24 |
800 |
600 |
0,3 d |
800 |
400 (Fkl. - 040) |
Untere
Streckgrenze Rel oder 0,2% - Dehngrenze Rp 0,2 bei 100 °C = 85 % bei 200 °C = 80 % bei 300 °C = 75 % bei 400 °C = 70 % |
* Diese Werte gelten nur für Verbindungselemente (Schrauben) mit Längen bis 8 x Gewinde-Nenndurchm. (8 x d) ! |
Tabelle 34: Festigkeit von Edelstahl
Für Sechskant-, Innensechskant-, Schlitz- und Kreuzschlitzschrauben ist die Festigkeitsklasse - 70 der Regelfall und handelsüblich. Verbindungselemente aus nichtrostenden Stählen sind kaltzäh und gut geeignet für den Einsatz bei tiefen Temperaturen (A 2 bis -200 °C, A 4 bis -60 °C nach DIN 267-13).
Austenitische Werkstoffe sind nicht durch Wärmebehandlung härtbar - Verbindungselemente aus austenitischen Werkstoffen (A 1 - A 5) haben daher ein anderes Montageverhalten als vergütete Stahlschrauben. Unsachgemäße Montage kann zum Versagen (Kaltverschweißung/Fressen/Bruch) führen. |
! |
Magnetische
Eigenschaften von Edelstahl Verbindungselemente aus nichtrostenden Stählen sind im allgemeinen nicht magnetisierbar - durch die Fertigung kann eine Magnetisierbarkeit eintreten; wenn besondere Anforderungen an die Magnetisierbarkeit gestellt werden, muss dies entsprechend vereinbart werden. |
! |
Oberflächen von Verbindungselementen aus nichtrostenden Stählen
müssen sauber und metallisch blank sein.
(Passivierung =>ISO 16048)
4.4.3 Strecklastgrenzen von Edelstahlschrauben (nach oben)
Strecklastgrenzen für Schaftschrauben
Edelstähle vom Typ "A" sind nicht härtbar. Jedoch kann durch
Kaltverfestigung eine höhere Streckgrenze bewirkt werden. Angaben gem.
DIN EN ISO 3506
Durchmesser |
Strecklastgrenzen
in (Nm) |
|
50 (z.B. A2-50) |
70 (z.B. A2-70) |
|
M 5 |
2.980 |
6.390 |
M 6 |
4.220 |
9.045 |
M 8 |
7.685 |
16.470 |
M 10 |
12.180 |
26.100 |
M 12 |
17.700 |
37.935 |
M 16 |
32.970 |
70.650 |
M 20 |
51.450 |
110.250 |
M 24 |
74.130 |
88.250 |
M 27 |
96.390 |
114.750 |
M 30 |
117.810 |
140.250 |
Tabelle 35: Strecklastgrenzen für Edelstahlschrauben
4.4.4 Mindestbruchgrenzen von Edelstahlschrauben (nach oben)
Gewinde |
Mindestbruchdrehmoment
(Bmin) in Nm |
||
50 |
70 |
80 |
|
M 1,6 |
0,15 |
0,2 |
0,24 |
M 2 |
0,3 |
0,4 |
0,48 |
M 2,5 |
0,6 |
0,9 |
0,96 |
M 3 |
1,1 |
1,6 |
1,8 |
M 4 |
2,7 |
3,8 |
4,3 |
M 5 |
5,5 |
7,8 |
8,8 |
M 6 |
9,3 |
13 |
15 |
M 8 |
23 |
32 |
37 |
M 10 |
46 |
65 |
74 |
M 12 |
80 |
110 |
130 |
M 16 |
210 |
290 |
330 |
Tabelle 36
4.4.5 Hochtemperatur-Eigenschaften von Edelstahlschrauben (nach oben)
Durchmesser |
Warmstreckgrenzen, gemessen in N |
||||
+ 20 °C |
+ 100 °C |
+ 200 °C |
+ 300 °C |
+ 400 °C |
|
M 5 |
6.390 |
5.432 |
5.112 |
4.793 |
4.473 |
M 6 |
9.045 |
7.688 |
7.236 |
6.784 |
6.332 |
M 8 |
16.740 |
14.000 |
13.176 |
12.353 |
11.529 |
M 10 |
26.100 |
22.185 |
20.880 |
19.575 |
18.270 |
M 12 |
37.935 |
32.245 |
30.348 |
28.451 |
26.555 |
M 16 |
70.650 |
60.053 |
56.520 |
52.988 |
49.455 |
M 20 |
110.250 |
93.713 |
88.200 |
82.688 |
77.175 |
M 24 |
88.250 |
75.013 |
70.600 |
66.188 |
61.775 |
M 27 |
114.750 |
97.538 |
91.800 |
86.063 |
80.325 |
M 30 |
140.250 |
119.213 |
112.200 |
105.188 |
98.175 |
Tabelle 37: Hochtemperatur-Eigenschaften von Edelstahlschrauben
4.4.6 Reibungszahlen für Edelstahlschrauben/ -Muttern (nach oben)
Durch Schmierung kann die Reibungszahl, und damit die wichtigste Variable für das Anzugsdrehmoment sehr stark verändern. Grundsätzlich gilt, dass die Reibungszahl µ sinkt, wenn ein Schmiermittel verwendet wird. Daher kann bei Schmierung leichter ein "Abreißen" der Edelstahlschrauben eintreten, wenn mit gleicher Kraft wie bei einer ungeschmierten Verbindung angezogen wird.
Es gilt: Schmiermitteleinsatz >> Reibungszahl µ sinkt >>
weniger Anzugsdrehmoment ("weniger Kraft") ist nötig
Schrauben und Gegenlage aus |
Mutter aus |
Schmiermittel |
Nachgiebigkeit der Verbindung |
Reibungszahlen |
||
unter Kopf |
im Gewinde |
|
unter
Kopf |
im
Gewinde |
||
A2 oder A4 |
A2 oder A4 |
ohne |
ohne |
sehr groß |
0,35 - 0,50 |
0,26 - 0,50 |
Schmiermittel (z.B. Chlorparaffin-Basis) |
0,08 - 0,12 |
0,12 - 0,23 |
||||
Schutzfett gegen Korrosion |
0,25 - 0,35 |
0,26 - 0,45 |
||||
ohne |
ohne |
klein |
0,08 - 0,12 |
0,23 - 0,35 |
||
Schmiermittel (z.B. Chlorparaffin-Basis) |
0,08 - 0,12 |
0,10 - 0,16 |
||||
AlMgSi |
|
ohne |
sehr groß |
0,08 - 0,11 |
0,32 - 0,43 |
|
Schmiermittel (z.B. Chlorparaffin-Basis) |
0,08 - 0,11 |
0,32 - 0,43 |
||||
0,08 - 0,11 |
0,28 - 0,35 |
Tabelle 38: Reibungszahlen für Edelstahlschrauben
4.5 Kennzeichnung von Edelstahl (nach oben)
Klassifizierung von Edelstahl, z.B. A2-70 (Standard-Edelstahl)
A | Kennzeichen Werkstoffgruppe A = Austenitischer Edelstahl (Chrom-Nickel-Stahl) |
2 | Kennzeichen Stahlgruppe 1 = Automatenstahl 2 = Kaltstauchstahl legiert mit Chrom und Nickel (klassischer Edelstahl) 3 = Kaltstauchstahl mit Chrom und Nickel legiert und gehärtet mit Titan, Niob und Tantal 4 = Kaltstauchstahl mit Chrom, Nickel und Molybdän (hochsäurebeständig) 5 = Kaltstauchstahl mit Chrom, Nickel und Molybdän (hochsäurebeständig) und gehärtet mit Titan, Niob und Tantal |
-70 | Festigkeitsangabe: Zugfestigkeit Regelzugfestigkeit für 50 = 1/10 der Zugfestigkeit (mindestens 500 N/mm²) A1 70 = 1/10 der Zugfestigkeit (mindestens 700 N/mm²) A2, A4 (Standard) 80 = 1/10 der Zugfestigkeit (mindestens 800 N/mm²) A4-80, A5 |
Kennzeichnung von Edelstahlteilen
Die Normung geht bei
Produkten aus nichtrostenden Stählen von einer Kennzeichnungspflicht aus,
welche Schrauben ab 5 mm Durchmesser betrifft und Stahlgruppe, Festigkeitsklasse
und Herkunftszeichen enthalten muss.
bei Sechskantschrauben |
bei Zylinderschrauben mit
Innensechskant |
bei Muttern Die
Kennzeichnung durch Einkerbung verliert an Bedeutung, da dieses Verfahren
die Ränder der Muttern verletzt. Zwei Kerben stehen für A2,
vier Kerben für A4. Nicht gekennzeichnete Muttern oder Schrauben erfüllen meist nur die Festigkeitsklasse 50. |
|
Alle Angaben ohne Gewähr, Irrtümer und Druckfehler vorbehalten. Die Kommerzielle Benutzung von Text und Bild ist nur mit vorheriger schriftlicher Zustimmung erlaubt. Bilder und PDF-Dateien enthalten digitale Signaturen, die auch teilweise oder verändernde Entnahme nachvollziehbar machen.